Factory automation has long been the cornerstone of efficient manufacturing. Traditionally, this meant fixed robotic arms, conveyor belts, and rigid production lines. However, as market demands become more dynamic and supply chains more complex, manufacturers are seeking flexible, scalable, and intelligent automation solutions. One of the most transformative innovations in this space is the use of mobile robots—particularly Autonomous Mobile Robots (AMRs) and Automated Guided Vehicles (AGVs).
These robots are reshaping how goods move within factories, enabling greater agility, productivity, and efficiency. From transporting raw materials and parts to delivering finished products and supporting human workers, mobile robots are becoming essential to the modern factory floor.
What Are Mobile Robots in Factory Automation?
Mobile robots are robotic platforms capable of moving freely within a factory environment. Unlike traditional stationary robots, mobile robots are designed to navigate complex layouts, avoid obstacles, and interact with people and equipment dynamically.
There are two main categories:
- Automated Guided Vehicles (AGVs): These follow predefined paths, such as magnetic strips, wires, or QR codes. AGVs are reliable but require infrastructure and offer less flexibility.
- Autonomous Mobile Robots (AMRs): These use sensors, cameras, LiDAR, and AI algorithms to navigate freely. AMRs can dynamically plan routes, avoid obstacles, and adapt to changes in the environment without human intervention.
How Mobile Robots Transform Factory Automation
1. Intralogistics Optimization
One of the most significant applications of mobile robots in factories is material handling. They can transport components, tools, packaging, or finished goods across various zones—between receiving docks, assembly stations, warehouses, and shipping areas.
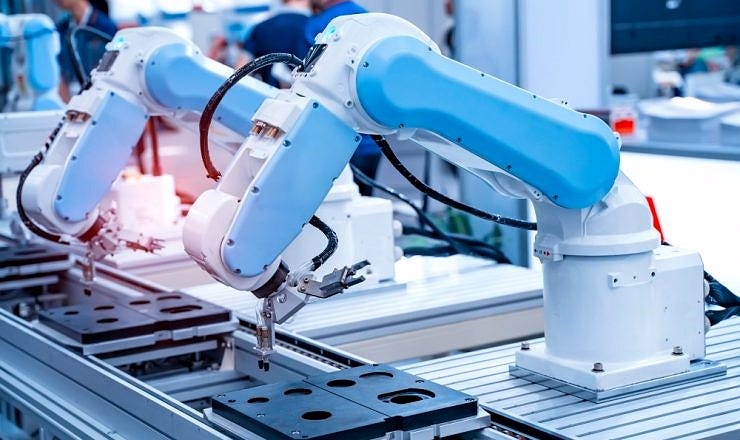
By automating intralogistics:
- Manual transport tasks are eliminated.
- Operators can focus on higher-value work.
- Material flows become more predictable and traceable.
2. Production Line Support
Mobile robots can support assembly lines by delivering parts or removing completed subassemblies. They are often used in just-in-time (JIT) and just-in-sequence (JIS) production systems to ensure the right components arrive at the right place and time.
This flexibility allows manufacturers to scale up or reconfigure production lines without extensive downtime or infrastructure changes.
3. Inventory and Warehouse Automation
Mobile robots can also perform automated picking, stock replenishment, and inventory tracking. Integration with warehouse management systems (WMS) and enterprise resource planning (ERP) systems enables seamless inventory updates in real-time.
Some mobile robots are even equipped with robotic arms to pick items from shelves, making them effective in hybrid factory-warehouse environments.
4. Human-Robot Collaboration
Unlike many industrial robots that require safety cages, AMRs are designed to operate safely alongside humans. Using smart sensors and safety protocols, they can detect and avoid people, making them ideal for collaborative environments.
They act as “robotic coworkers” that take over physically demanding or repetitive tasks, improving ergonomics and reducing the risk of workplace injuries.
Benefits of Mobile Robots in Factory Automation
1. Flexibility and Scalability
Mobile robots are highly adaptable. Unlike fixed automation systems, they can be quickly reprogrammed or re-routed. This is crucial for:
- High-mix, low-volume manufacturing
- Changing production layouts
- Seasonal demand surges
Adding more robots is as simple as deploying new units with minimal changes to existing infrastructure.
2. Cost Efficiency
Although there is an upfront investment, mobile robots deliver fast ROI by reducing labor costs, increasing productivity, and minimizing downtime. They also reduce errors and improve process consistency.
Because AMRs don’t require dedicated tracks or complex infrastructure, they reduce installation and maintenance costs compared to AGVs or conveyors.
3. Enhanced Data and Analytics
Modern mobile robots are connected devices that collect and transmit data on their activities, battery health, usage patterns, and environmental conditions. This data can be used to:
- Optimize routes and workflows
- Predict maintenance needs
- Measure performance KPIs
The result is data-driven decision-making for continuous improvement.
4. Labor Shortage Mitigation
Manufacturers worldwide are facing skilled labor shortages. Mobile robots fill the gap by automating mundane tasks, allowing human workers to focus on complex or creative work.
This can improve job satisfaction and make manufacturing roles more appealing to a new generation of tech-savvy workers.
Key Technologies Behind Mobile Robots
1. Navigation and Mapping (SLAM)
Simultaneous Localization and Mapping (SLAM) enables AMRs to build maps of their environment and localize themselves within it. This allows them to:
- Operate in dynamic environments
- Avoid collisions
- Replan routes in real-time
2. AI and Machine Learning
Mobile robots use machine learning to improve navigation, obstacle avoidance, and task performance over time. AI also supports predictive maintenance and operational optimization.
3. IoT and Cloud Connectivity
Integration with IoT systems allows real-time monitoring and fleet management. Cloud platforms offer centralized control and analytics dashboards for performance visibility across facilities.
4. Human-Machine Interfaces (HMI)
User-friendly HMIs enable operators to assign tasks, monitor progress, and interact with robots without programming skills. Mobile apps and web dashboards are increasingly common.
Challenges in Deploying Mobile Robots
Despite the advantages, there are some challenges:
- Initial Costs: The investment in robots, integration, and training can be substantial.
- Integration Complexity: Mobile robots must communicate with existing systems (ERP, WMS, MES).
- Change Management: Operators and managers need training to adapt to robot-supported workflows.
- Safety and Regulation: AMRs must comply with safety standards, and risk assessments are essential.
Addressing these challenges requires strategic planning, pilot projects, and cross-functional collaboration.
Real-World Applications and Case Studies
1. Automotive Manufacturing
Car manufacturers use AMRs to deliver components to assembly lines in a just-in-time fashion. Mobile robots enhance flexibility in highly modular and complex production systems.
2. Electronics and Consumer Goods
Facilities producing high-mix, low-volume items use AMRs to adapt to frequent product changes. Robots transport parts, handle packaging, and support quality control.
3. Food and Beverage Industry
In cleanroom or temperature-controlled environments, mobile robots maintain hygiene and consistency. They help in transporting raw ingredients, packaging, and finished goods.
4. Pharmaceutical Manufacturing
AMRs are used to move medicines, sterile equipment, and samples between cleanroom environments, ensuring compliance with stringent regulations.
The Future of Mobile Robots in Factory Automation
The market for mobile robots is growing rapidly. According to industry research, the global AMR market is expected to grow at a CAGR of over 20% in the next five years. The future holds:
- Greater Autonomy: Robots that can make more complex decisions independently.
- Swarm Intelligence: Fleets of robots working cooperatively for optimized logistics.
- Integration with AI vision systems for inspection and quality control.
- 5G connectivity for ultra-fast communication and edge computing capabilities.
As factories become smart and connected, mobile robots will play a central role in enabling autonomous, responsive, and self-optimizing production systems.
Conclusion
Mobile robots are a powerful enabler of next-generation factory automation. They offer the flexibility, intelligence, and scalability required to meet the demands of modern manufacturing. By optimizing intralogistics, supporting production lines, and collaborating safely with humans, mobile robots are not just tools—they are becoming essential team members on the factory floor.
As technology continues to evolve, their capabilities will only expand, making them integral to the future of smart, efficient, and resilient manufacturing ecosystems.